Asset Care Management System
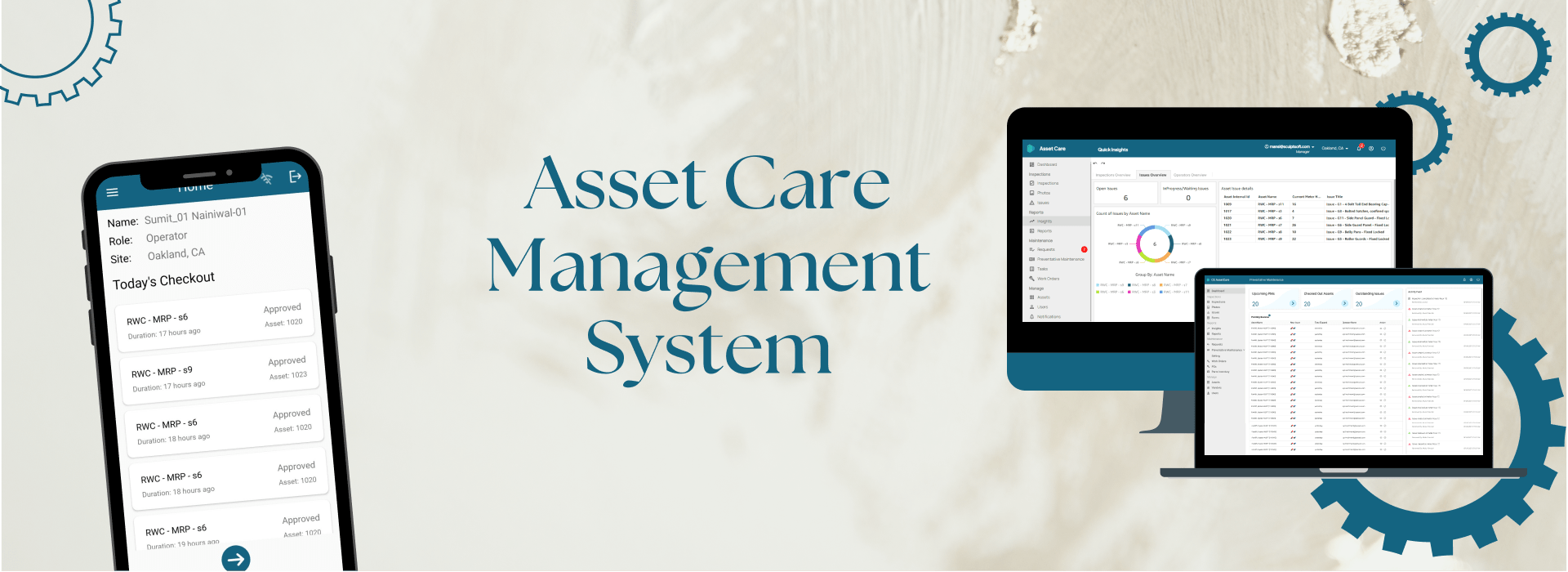
About Client
Industry
Automotive and Transportation
Location
USA
Project Overview
Traditional Fleet Maintenance Process
01
02
03
04
05
06
07
08
09
10
11
12
Challenges In Traditional Fleet Maintenance Process
01
02
03
04
05
06
07
08
09
09
10
Our Solution - Asset Care Management System
01
02
03
04
05
06
07
07
Outcome - This Is How Our Client Benefited
Reduced Downtime: Unplanned downtime decreased significantly as preventive maintenance schedules were optimized, reducing the likelihood of unexpected breakdowns.
- Downtime Reduction: 30%,
- Average Downtime per Vehicle After Implementation: 10.5 hours per year
Cost Savings: The ability to track maintenance costs and optimize preventive maintenance led to cost savings in terms of reduced emergency repairs and improved operational efficiency. Annual Maintenance Cost Reduction: 15-20%
Improved Safety Compliance: The Asset Care Management System ensured that vehicles were regularly inspected and maintained, contributing to improved safety compliance with regulatory standards.
- Compliance Violation Reduction: 25%,
- Annual Compliance Violations After Implementation: 9 incidents.
Enhanced Tracking and Reporting: Managers had real-time visibility into the maintenance status of each vehicle, allowing for proactive decision-making and resource allocation.
Streamlined Operations: Work order management and Inspections through a web app and mobile app respectively streamlined communication between operators, Managers and the maintenance team, improving overall efficiency.
- Operators Productivity Increase: 25%
- Average Tasks Completed per Day per Technician After Implementation: 6.25
Features
Asset Inspections
User Management
Asset Management
Notifications
Inspections
Issues Generated from Inspection
Inspection Photos
AWS Quicksight for Insight of System
Maintenance Requests
AWS Quicksight for Insight of System
Preventative Maintenance for Maintenance Scheduling
Activity logs
Work Order Management
Reports
- Asset Report
- Asset Inspection Report
- Latest Meter Hour Reading Reports
Technology Stack
Database
- PostgreSQL
Frontend
- React JS
- HTML
- CSS
- JQuery
- Google Maps API

Backend
- Xamarin Forms
- MVVM architecture
- Firebase Push Notification
Server
- AWS Cloud
Third party Integration
- AWS S3
- Sentry
- SendGrid
- Appcenter
AWS Infrastructure and Services
- ECS
- Amplify
- Quicksight
- Lambda Functions
- SQS Service
- AWS Cognito
- Gitlab with Openvpn